HP SERIES
Hot Press
Part of a long standing tradition of quality, dependability, and innovation in high temperature vacuum and controlled atmosphere heating technology.
HP SERIES Hot Press
Centorr/Vacuum Industries Hot Press Sintering Furnaces are part of a long standing tradition of quality, dependability, and innovation in high temperature vacuum and controlled atmosphere heating technology.
The hot press furnaces' hot zone is resistance heated (induction systems available), and is thermally insulated from the cold-walled vessel by a multi-layer configuration of metallic radiation shields, or fibrous graphite insulation. Access to the hot zone for loading/unloading, as well as for routine maintenance and inspection is through the full opening front door. Clamps are provided for operation at slightly positive pressures (up to 2 psig).
The inside of the furnace chamber conforms to the best vacuum and controlled atmosphere practices, with particular attention given to the surface finish and choice of materials. The design and construction of high-quality furnaces calls for minimizing component surface area and potential leaks; thus you won't find inferior metals or ceramic refractory insulation in a Centorr/Vacuum Industries Hot Press furnace.
Visual observation of the process material is provided by a sight port equipped with the Centorr-designed rotatable quartz viewing glass. Ports are provided for gas inlet(s), thermocouples, gauges, and other pertinent instrumentation. All instrumentation is positioned in an attractive console for optimal monitoring and control. Furnace temperature is controlled by a closed-loop circuit between the temperature sensor (thermocouple, power transducer, or optical pyrometer), the control instrument, and the power supply. The entire furnace system is protected by a water-flow interlock that shuts down the hot zone if cooling water flow is reduced or closed off. Additional protection is provided by gas pressure or flow sensors which monitor the incoming process gases; unacceptable conditions trigger a visual and audible alarm.
These furnace systems are ready to operate as soon as connections are made to the proper utilities. Each Centorr/Vacuum Industries' Hot Press Sintering furnace is completely assembled and thoroughly tested before it is shipped.
Features
- Operation to 2500°C with temperature uniformity to ± 10°C in uniform effective hot zone. Specials to 3000°C.
- Ability to press compacts from 3" dia. to 20" diameters from partial pressures of 10-6 torr up to 0-2 psig positive pressures.
- Electric motor driven Hydraulic pumps designed to generate up to 3000 psig pressure for pressing forces from 100 ton up to 1500 ton.
- Stainless steel chamber, with appropriate hot zone (graphite or refractory metal).
- Power supply with silicon controlled rectifier, current limiter, and separate amp and volt meters.
- NEMA-1 control cabinet with wide-rack mounting for instrumentation.
- Water manifold circuit with safety interlock to protect against damage due to water failure.
- Automatic inert gas control for operation to 2 psig, with relief valve.
- Rough or high vacuum pumping system (mechanical, diffusion, turbo-molecular, or cryogenic), with graphic control panel.
- Programmable controller with optional computer interface.
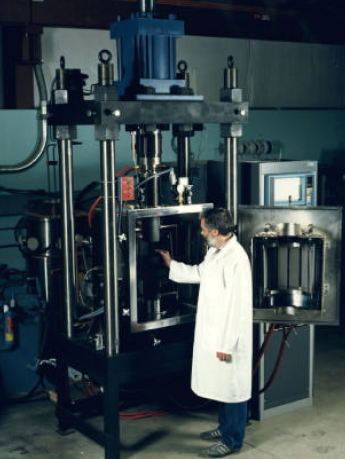
Model HP-12.5x14-W-M-10S7-A-17 100 Ton Post and Platen Vacuum Hot Press with refractory metal hot zone.
Specifications
STD MODEL* | 3x8 | 4x10 | 7x10 | 9x8 | 10x10 | 14x18 | 24x24 |
---|---|---|---|---|---|---|---|
Hot Zone Size Dia x H in (mm) | 3 x 8 (76 x 200) | 4 x 10 (100 x 250) | 7 x 10 (180 x254) | 9 x 8 (230 x 200) | 10 x 10 (254 x 254) | 14 x 18 (360 x 460) | 24 x 24 (610 x 610) Graphite Only |
Max. Die Diameter in (mm) | 2 (50) | 3 (75) | 5 (130) | 6 (152) | 7 (180) | 10 (254) | 20 (510) |
Max. Ram Force
lbs.
(kgs)
tons |
10,000 (4,500) 5 | 10,000 (4,500) 5 | 50,000 (22,675) 25 | 100,000 (45,350) 50 | 100,000 (45,350) 50 | 200,000 (90,700) 100 | 300,000 (136,000) 150 |
Press Frame Style |
'H' frame for 5-25 tons, or 'Post and Platen' for 20-250 tons |
||||||
Atmospheres |
High Vacuum, Rough Vacuum, Inert Gas or Hydrogen Gas |
||||||
OPTIONS | |||||||
Ram Control | Manual (1%)** | Coarse (1%)** | Precise (0.5%)** | ||||
force
position
controller |
Pressure Control Valve Dial Indicator (0.001) None | Pressure Transducer Linear cable transducer (0.015) Microprocessor | Load Cell Linear non-contact transducer (0.0005) Microprocessor | ||||
Temperature °C (°F) | 1200°C - 1900°C (2200°F - 3450°F) Thermocouples | 900°C - 2300°C (1650°F - 4175°F) Optical Pyrometers |
*Custom sizes available upon request
**Accuracy measured as a percent of max ram force.
Options
- Precision force and travel control
- Adjustable x-y axis post and platen frame or rugged 'H-Frame' designs for pressing at max pressures with minimal deflection.
- Uses bellows or sliding shaft seal on rams, depending on process requirements.
- extra heavy-duty actuators.
- Fully automatic cycle control
- Optional hot rods, platens, punch & dies
- Thermally isolated hot rods to reduce power consumption.
- CE / VDE / TüV / CSA approvals and other non-U.S. standards for compliance.
- Gas fan recirculation system with integral heat exchangers available.
- Optional Binder Removal Systems consist of thermal oxidizer or Vacuum Sweepgas™ method for low cost efficient binder removal.
- PLC with Industrial Programmable Controller or PC system using Intellution™ FIX32 HMI software customized by C/VI for vacuum furnaces, with extensive data acquisition, and remote operation capabilities.
- Single or Double-acting rams available with option for "hot ejection" - the hot compact can be ejected from the die to reduce the cooling time by up to 50% and minimize die sticking or scoring.
Applications
- Hot compacting of carbide, oxide, and nitride mixtures
- Development of ceramic composite materials
- Diffusion Bonding studies
- Metal Matrix bonding
- Development of superconductors
- Allows compaction close to theoretical densities of most metals and ceramics

Contact Us
800.962.8631
603.595.7233