Centorr Vacuum Industries
About Us
Since 1954 CVI has introduced many industrial high temperature vacuum furnace solutions for production and R&D. Centorr Vacuum Industries is a manufacturer of high temperature vacuum and controlled atmosphere furnaces with an installed base of over 6500 units worldwide
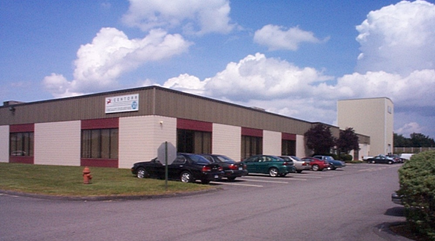
Centorr Vacuum Industries is a manufacturer of high temperature vacuum and controlled atmosphere furnaces with an installed base of over 6500 units worldwide. Our furnace offering ranges from large commercial and production units with hot zones over 3m x 3m, to smaller Laboratory and Research & Development furnaces for use at temperatures up to 3500°C.
While many of our furnaces are standard designs and sizes, we also offer custom-built equipment specialized to individual customer requirements.
Our Sales and Manufacturing offices are located in Nashua, NH USA and include a fully staffed Sales and Aftermarket Field Service group, and we operate an Applied Technology Center offering R&D support and toll firings services.
For more information please contact the sales department at 603-595-7233 or on the web using the form at right.
Company Profile & Technology
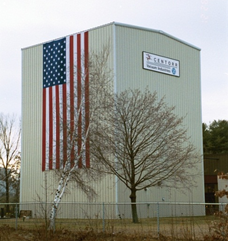
Market Achievements/Process Offering
Centorr Vacuum Industries' leading position has been achieved through high quality engineering and manufacturing to reinforce experienced product management for the application fields served. Centorr Vacuum Industries has introduced many furnace solutions over the years. which have included:Year | System/Equipment | Process/Product |
---|---|---|
1954 | Retort Furnace, In-Situ Cooling Arc Melting Furnace Induction Melting Furnace Vacuum Hot Press Hi-Temp. CVD Resistance Furnaces | Annealing titanium Nuclear reactor fuel alloys Nuclear reactor fuel alloys Ceramics composite research Pyrographite deposition |
1961 | 10 Meter Long Furnace with vacuum cooling chamber Semicontinuous Carousel Furnace with load lock | Annealing Titanium Sintering tungsten carbide |
1964 | First Multipurpose Vacuum Furnace SYSTEM VII Physical Test Furnace | Gen. Purpose - heat treat, melt, weld, braze Physical test of materials in controlled atmosphere and temperature |
1966 | Resistance Cold Wall Furnaces with gas quench | Production vacuum heat treating |
1967 | Crystal Growth Furnace | Adjustable gradient furnace |
1969 | Immersion Platen Diffusion Bonding Press | Aircraft components |
1975 | Fiber Draw | Fiber optic drawing furnace |
1977 | 30 Meter Long Horizontal Furnace | Thermal treatment - Inconel tubing |
1979 | Vacuum Induction Melt Semi-continuous | Equiax and directional solidification for investment casting |
1982 | Vacuum Sintering Furnace Belt Furnace | PM tool steels Continuous operation above 1200°C |
1985 | Production CVD Furnaces | Advanced ceramics |
1987 | Injectavac™ Sintering Furnace Diffusion Bonding Hot Press | PM injection-molded components Pour ram 42x42, 250 Ton-Turbine Blades |
1989 | Rotavac™ | Rotary furnace for refining powders |
1991 | Testorr™ Materials Testing Furnace | Materials mechanical testing |
1992 | Injectavac II™ | 500 kg. P/M parts - brazing |
1993 | Transparent Furnace Introduction | See-through furnace |
1994 | Tungsten Mesh Belt Furnace | Patent Awarded |
1995 | High Pressure/Temperature with Dilitometer Controlled Atmosphere Sealing Furnace | Growth studies on high performance materials lighting industry |
1996 | High Capacity Graphitization Furnace Continuous Debind/Sintering of non-oxide ceramics in revolutionary design Pusher Furnace | 2600°C - 8'x10', Turnkey Installation 2500°C |
1997 | Fiberdraw 11 B/E Preform Consolidation | Higher capacity fiber drawing with improved process control Glass consolidation for fiber drawing |
1998 | High Capacity CVI for CFC Fiberdraw for 80mm Preform Continuous tantalum capacitor sintering furnace Fiberdraw for low temperature applications | 2750°C - 50" x 52" Improved fiber quality and run length Improved quality throughput 350°C |
1999 | Metal Hot Zone MIM - Generation 1 design | Processing of high purity SS/Ti MIM |
2000 | Large 2300°C/300Ton Vacuum Hot Press Large 2300°C SiC Debind & Sinter design with high output thermal incinerator | 2300°C processing of non-oxide ceramics 2300°C processing of large SiC parts |
2001 | High Capacity 25 cu ft (0.73cm3) Tungsten Carbide Sinter Furnace | Uniformity of ±2.5°C |
2002 | Large Scale Crystal Growth Furnace Design | Processing of delicate materials in high volumes |
2003 | State-of-the-art CVD System for SiC/MTS Intellution HMI/PLC Control Strategy furnace designs | New Liquid Injection Dosing system Executed for batch and continuous |
2004 | Vacuum Equipment for Nuclear Materials | Custom vertical and horizontal vacuum furnaces for proprietary applications |
2005 | 40' (12m) Hot Wall/Cold Wall Vacuum Furnaces for Tube Heat Treatment Remote I/O Design Strategy | Difficult processing requirements Minimizes furnace wiring and installation times |
2006 | Commercialize 2nd Generation 'Modular' MIM furnace | Achieved ±0.5° uniformity with precision gas/vacuum control |
2007 | Provides 5 Armor Furnaces for non-oxide ceramics to 4 different manufacturers | Sizes varied from2 cu ft. to 50 cu ft. with debind and sinter capability |
Six 2900°C heat treat furnaces provide for Carbon/Graphite work | 100 cu ft size with cold traps and fast cooling package | |
Introduce new low-cost LF-15 Furnace for R&D Introduce new interchangeable hot zone Hot Press | 2000°C capability in low/high vacuum Used for metals and ceramics testing | |
2008 | 90ft. (28m) Cold Wall Vacuum Furnace for Annealing Large 140 cu ft size Graphite Sintering furnace | Large International Contract for China For diesel particulate filtration market |
2009 | 2900°C Production size Bottom Load heat treat furnaces provided for Carbon/Graphite work | 30" dia x 40" size with fast cooling package |
Five (5) Ceramic Sintering Furnaces of various sizes for SiC sintering | CVI leads sales of equipment in Ceramics | |
2010 | 90ft. (28m) Cold Wall Vacuum Furnace for Tube Annealing Two (2) 600kgs Ceramic Sintering Furnaces for B4C Armor sintering | Large International Contract for Japan CVI's proprietary gas system design is favored by Industry leaders. |
2011 | Sapphire Annealing Market Continued Growth in Ceramic Sintering | Multiple unit orders for Asia and USA Larger size debind and sintering units sold |
2013 | Introduced 2nd Generation Workhorse furnace line Commercialized low cost HMI control system | Improved design with lower pricing Based on Specview/Yokogwa Platform |
2016 | Offered new 2BAR gas quench Heat Treat Lab unit Commercialized low cost HMI control system Developed units for AIN Substrate business | Sold to world leaders in Aviation Engine Market Based on Specview/Yokogawa Platform to support growsing LED market |
Customer Base
Users of Centorr Vacuum Industries' furnace equipment include leading government and private research organizations, universities, and manufacturing firms engaged in processing existing materials for improved properties or developing entirely new types of materials. With over 6500 systems installed, Centorr Vacuum Industries has an established reputation for supplying advanced design high-temperature vacuum and controlled environment processing equipment which is expertly crafted and field-proven for dependable operation. We look forward to the opportunity to work with you and be of service on your vacuum furnace opportunity.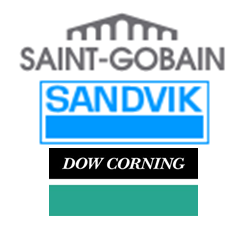
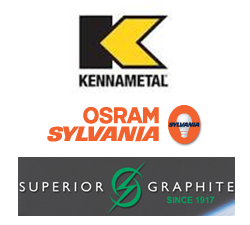
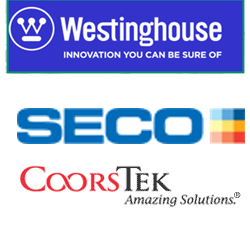
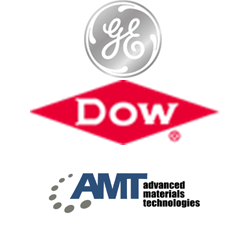
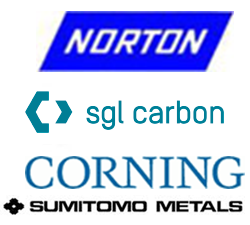
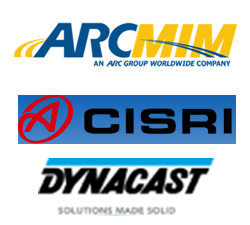
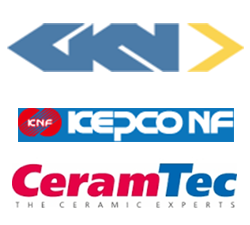
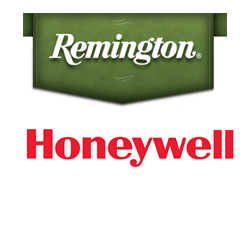
Meet the CVI Team
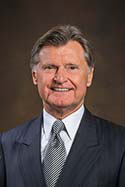
Bill Nareski is the Chief Executive Officer and controlling shareholder of Centorr Vacuum Industries. He brings a distinguished career which includes both operational management and corporate development positions. His direct line experience includes engineering, sales, marketing, and finance. Bill has also managed the successful U.S. market introduction of vacuum related equipment for Ulvac Ltd. and served as an electrical engineer for the Missile Systems Division of Raytheon. Bill has an M.B.A. from Harvard University and B.S. and M.S. degrees in Electrical Engineering from Rensselaer Polytechnic Institute.
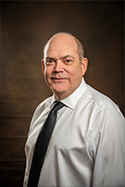
Randy joined Centorr in 1997 as an Electrical Engineer and quickly rose to the Manager of the Electrical Engineering Department. Skilled in all instrumentation and controls technologies Randy lead CVI’s efforts into computer controlled HMI implementation in the early 2000’s. Randy had worked previously for Saint-Gobain Diamond Film where he headed the Furnace Deposition Team and gained years of practical furnace experience. He became COO of Centorr in 2023. Randy has a B.S. in Computer Science from Franklin Pierce College and two AS degrees in Industrial Electricity and Industrial Electronics.
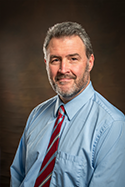
Ernie joined Centorr Vacuum Industries in 2015 as Director of Engineering. Knowledgeable in a variety of high-temperature applications, he has worked in the vacuum furnace industry since 2009 and has experience in crystal growth, gas pressure sintering, and a variety of Ceramics and Metals processes. Ernie has a degree in Mechanical Engineering from the University of Massachusetts, Lowell, and an MBA from Plymouth State University. He is a member of the National Fire Protection Agency (NFPA).
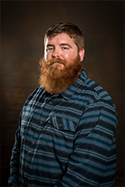
Justin has been with Centorr Vacuum Industries since 2016. He started in the Manufacturing group doing Furnace Assembly for 2 years, and then moved into Field Service where he worked until 2022 performing job start-ups, in house testing, in field troubleshooting, and customer Preventative Maintenance Services. As Operations Manager he is involved in every phase of vacuum furnace construction from initial design to final manufacturing, while overseeing the entire manufacturing process for Centorr Vacuum Industries.
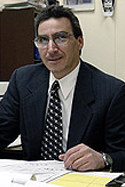
Vinny has been with Centorr Vacuum Industries since 1974, having started as a sawyer in the manufacturing department. He is involved in every phase of vacuum furnace construction from initial design to final manufacturing and oversees the entire manufacturing process and Purchasing functions for Centorr Vacuum Industries.
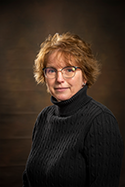
Kellie has been with Centorr Vacuum Industries since 2002 and has a B.S. degree in Accounting/Finance from Southern New Hampshire University. Kellie worked in the human resource management industry for 13 years prior to joining Centorr. In 2023 she was promoted to the Vice President of Administration including Human Resources and IT, and is the company Controller.
Brianna started with Centorr Vacuum Industries in 2015 in the purchasing department, and in 2017 was promoted to Purchasing Manager. She has her BA in Business Management from University of Phoenix and her MBA from University of Phoenix. Brianna is responsible for the Purchasing department and oversees all facets of the ordering process for CVI.
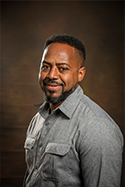
Nelson completed his education in the US Virgin Islands, with a focus on Supervisor and Leadership training. He has worked for Centorr Vacuum Industries since 2016 in the Field Service group and was promoted to Manager of the Department in 2022. Nelson has been involved in the vacuum furnace industry since 2004 in Field Service support, and in management of a Field Service Department since 2010.
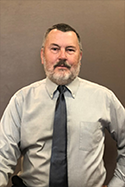
Alan graduated from Franklin Pierce College in Rindge, New Hampshire and holds a degree in Public Administration. He started with the Aftermarket Services Department of Centorr Associates in 1987 and continued on with Centorr Vacuum Industries in 1990. Alan is responsible for Aftermarket sales and service for the Centorr product line.
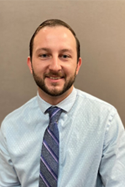
Joe has been with CVI since 2014, initially as the QC Coordinator in Quality Control. In 2016 he transferred into the Purchasing department as the Aftermarket Sales Buyer/Planner and in 2022 moved into the Aftermarket Sales department handling Spare Parts sales and retrofits for the Production Vacuum Furnace line for Centorr Vacuum Industries, as well as responsibility for the Applied Technology Center Toll Laboratory. Joe is working on his Associates Degree in Business Administration from SNHU University.
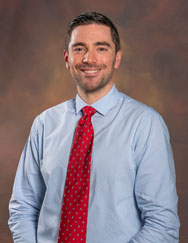
Sean attended Alfred University's SUNY College of Ceramics with a degree in Materials Science and has an MBA from Southern NH University. He joined CVI in 2024 and has 15 years experience in the manufacturing of advanced ceramics for the automotive electronics industry and will be responsible for over thirty (30) different product lines used in laboratory settings for the metals, ceramics, and carbon/graphite/composites industries. Sean has experience with a number of different vacuum furnace technologies including Hydrogen sintering, spark plasma sintering, and annealing, and he is a member of the American Ceramic Society, MPIF, APMI, and MIMA.
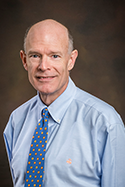
Scott attended Alfred University's SUNY College of Ceramics with a degree in Ceramic Engineering. He has been with Centorr Vacuum Industries since 1999 and has worked in the furnace and refractories industry since 1984. He handles the Production sized batch and continuous furnaces for Ceramics, Hardmetals, Carbon, Graphites & Composites, Nuclear materials, as well Metals processes including Brazing, Annealing, Heat Treating, PM Sintering, and Metal Injection Molding. Scott is a member of the American Ceramic Society, Keramos, MPIF, APMI, and MIMA.
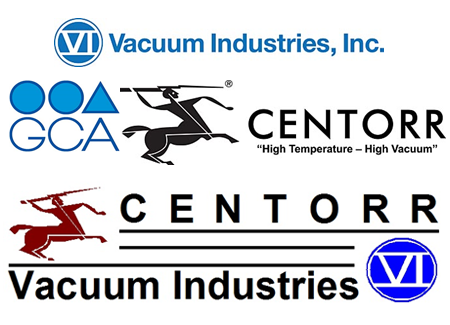
[email protected] | (603) 595-7233
Thank you for visiting www.centorr.com

Contact Us
800.962.8631
603.595.7233