SINTERVAC HIGH-TEMPERATURE VACUUM FURNACE FOR PROCESSING ADVANCED GRAPHITE MATERIALS
Nashua, NH, 27 April 2020-
Centorr Vacuum Industries developed its first high-temperature vacuum and controlled atmosphere furnaces for Ceramic sintering in the 1960’s. More recently Centorr has worked very closely with a customer in the graphite industry on an application requiring a high temperature degass and heat treatment. The furnace solution was a small production sized unit with 2 cu ft capacity, rated to 2450°C operation, which was matched to the annual production volumes of the customer.
For this operation, the low temperature capability of the furnace was used to degass the raw material and the Sintervac C allows the customer to perform this process in either partial pressures or positive pressures of inert gas flowthrough. Because of the presence of tarry binder offgassing as well as the possibility for particulate materials in the gas stream the customer can remove these materials in a specific partial pressure that is below the vapor pressure of the offgas material allowing for their safe removal using an inert gas sweepgas. The Sintervac was configured with a dual trapping system consisting of Centorr’s T/P trap (trap-over-pot design) which uses a water cooled jacket surrounding dual filtration media in and easy-to-remove basket. A second 10 micron filter canister is provided for removing very fine particulate that would otherwise pass into the pumping system.
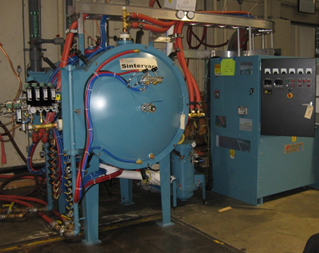
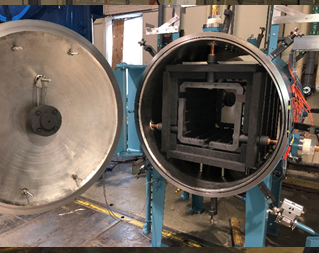
Later in the process when the customer is nearing temperatures over 2000°C, they can switch over to a positive pressure flowthrough of inert Argon gas to ensure there are no vapor pressure issues due to operating in vacuum. In this case the particulate laden gas flow also passes through the T/P trap before exiting through an exhaust manifold to be safely plumbed out of the customer’s facility. Because the hot gases must first pass through the water-cooled trap, their temperature is lowered significantly allowing it to leave the furnace without passing through a narrow passage water-cooled heat exchanger which would likely plug up with process offgassing. The robust wide-area manifold includes a dual branched exhaust tower with the second pipe providing a backup exhaust path in the case that the primary flow path is blocked. This robust design provides for more trouble-free operation and ensures that a majority of the process offgassing is removed before it can either pass into the vacuum pumps oil sump, or into the building exhaust system.
Operation of the furnace to max temperatures of 2450°C ensure that there is minimal process offgassing or metal oxides left on the graphite part’s outer surfaces providing for clean contaminant free parts.
Centorr Vacuum Industries is a high temperature vacuum / controlled atmosphere furnace manufacturer with an installed base of over 6500 units worldwide. Their furnace offering ranges from large commercial and production units with hot zones over 3m x 3m x 3m, to smaller Lab and Research & Development furnaces for use at temperatures up to 3500°C. They are located in Nashua, NH with a fully staffed Aftermarket Field Service group, and Applied Technology Center offering R&D support and toll production service. For more information please contact the sales department at 603-595-7233 or visit their website: www.centorr.com