3520 SERIES
Diffusion Bonding Hot Press
The Series 3520 is an integrated system capable of exerting a force up to 200 tons in vacuum or controlled environments.
Diffusion Bonding Vacuum Hot Press
This versatile Diffusion Bonding Hot Press is an integrated system capable of exerting a force up to 200 tons in vacuum or controlled environments at temperatures up to 2400°F on parts heated in an effective hot zone 8" wide x 12" high x 20" long.
Water cooled rams and a cold wall resistance furnace are loacted within the vacuum chamber. External press frame supports chamber, vacuum, and hydraulic pumping systems. Saturable-core reactor power supply with solid state linear power control provides low voltage power to heating elements. Platens up to 8" x 20" in a variety of materials are easily attached to the rams. With the platens removed and the rams withdrawn, the system may be used as a general purpose high-temperature vacuum furnace.
Features
- Joins material by simultaneous application of heat and pressure.
- Bonding occurs in solid state eliminating need for melting materials or melting point metal filler.
- Can be used as a general purpose high-temperature vacuum furnace.
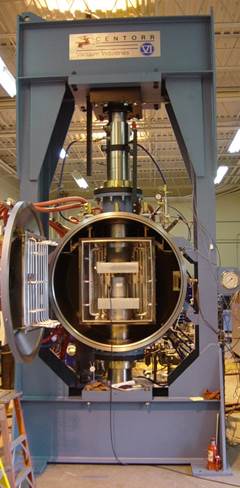
Specifications
Chamber | Horizontal, 30" diameter x 30" long stainless steel interior 100% jacketed with full-opening, hinged door with clamps, supported by press frame @53"CL elevation. Ports for power, rams, thermocouples, two 2 1/2" shuttered sight glasses, vacuum pumping and inert gas purge. | ||||||||||||
Press & Frame | Hydraulic press, double-acting with frame-mounted 3 stage hydraulic power unit with force/pressure regulator, advance, hold and reversing valve. Pressure gauges and relief valve. Pedestal and hydraulic rams are water-cooled, may be withdrawn to clear furnace for general use. Stroke 6 5/8". | ||||||||||||
Vacuum & Inert Gas System | 10" main valve air-operated failsafe closing; 10" 4300 l/sec. diffusion pump; multi-coolant chevron baffle; 50 CFM mechanical pump; 3.5 CFM holding pump; welded steel manifolding and vibration isolation, 3" manual roughing and fore valves; connections for gauges and leak detector; vacuum gauge control combination hot filament ionization and two-station thermocouple, 1 to 1000 microns and 1 micron to 2 x 10-7 torr. Inert atmosphere system includes 5 psig relief valve, 30"-0-15 psig Bourdon gauge, needle valve for gas inlet. Electrics include circuit breakers, pilot lamps, semiautomatic vacuum pump system controller, complete with function selector switch and keylock overrides mounted in NEMA-1 control cubicle. | ||||||||||||
Internal Mechanism | Furnace cold wall, refractory metal rod elements and inner heat shields. 6" diameter water-cooled ram shanks, 12&qot; daylight when full open without platens attached which act through 6" diameter sliding seals. | ||||||||||||
Power Supply | 75 kva, three-phase saturable core reactor with solid state linear power control. Includes furnace volt and current meters, cooling water flow interlock, shunt trip circuit breaker. | ||||||||||||
Temperature Controls (Optional) | 3-mode proportioning control with adjustable set point and strip chart recorder with Pt/Pt-10% Rh thermocouple. Separate indicating over-temperature indicator coutout with thermocouple. | ||||||||||||
Space & Service Requirements |
|
||||||||||||
Performance |
|
Applications

Contact Us
800.962.8631
603.595.7233