2500 SERIES ROTATING DRUM
Rotavac™ Furnaces
Improved Powder Material Processing. Rotating Retort Tumbles Powders at Temperatures up to 2300° C.
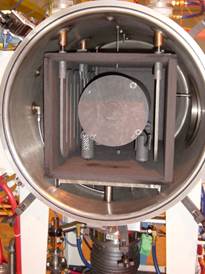
CALCINE...REACT...COAT...PURIFY
Do all the above and more in the new Rotavac™ furnace designed for lab scale powder processing. Its rotary drum retort constantly tumbles ceramic or metal powders, promoting uniform treatment, minimizing agglomeration.
Durms up to 8" dia. x 20" lg. (200 x 800 mm) are available in materials rated for temperature up to 2300°C. The drum rotation speed is infinitely variable from 0.1 to 10 rpm. Now, for the first time, powders can be processed in rotary retort at Ultra High temperatures.
Besides powder, preparation, the Rotavac™ furnace doubles as a 2300°C sinter/thermal processing furnace. Simply remove the retort, insert hearth and you're ready to sinter test shapes formed from the superior powders produced in the retort.
Operating from vacuum levels of 7.5 x 10-2 torr (10-1 millibar) to positive pressures up to 14.5 psig (2 bar), a wide range of processing atmospheres can be provided for desired powder properties.
Building on proven, quality components, a custom system is easily specified to meet your present process development needs while providing flexibility for future requirements.
Features
- Powder Consistency: Every particle exposed to uniform processing conditions.
- Product Purity: Volatiles removed in vacuum or swept away by gas.
- Rapid Cycle: Fast heat transfer in rotating retort
- Secondary Operation Eliminated: Free flowing product
- Versatility: Vacuum, inert reducing or oxidizing atmospheres
Specifications
Scaling Up For Production Once processing parameters have been established in the Series 2500 batch furnace, a full scale production furnace with continuous powder delivery and discharge capabilities can be specified. Custom designing or modifying standard furnaces to meet each end-user's individual requirements is Centorr Vacuum Industries' specialty. The CVI Technical Advantage Centorr Vacuum Industries' forty-plus years of experience in designing, building and testing vacuum and controlled environment furnaces is the technical advantage gained when you select CVI Rotavac™ furnace. During final furnace tests conducted before shipment, end-users are encouraged to participate. Instructions and drawings needed for installation, operation and maintenance are supplied with each furnace. Series 2500 Rotavac™ furnaces are simple to install, easily connected to your utilities. Field service technicians will inspect the original installation, supervise start-up operation and review operating procedures with plant personnel. Spares and maintenance parts are readily available and back-up service is available on short notice. Quality furnaces result from thorough process evaluation, superior design, careful manufacture and rigorous testing. CVI furnaces are your best investment for assured development capability and production continuity.Options
Retorts & Hot Zones- Graphite: up to 2300°C
- Alumina: up to 1650°C
- Stainless: up to 1000°C
Applications
- Ceramic Powders
- Nitriding
- Coating
- Calcining
- Purifying
- Reacting
- Metal Powers
- Carburizing
- Decarburizing
- Deoxidizing
- Annealing
- Degassing
- Coating

Contact Us
800.962.8631
603.595.7233